Exploring the Applications and Benefits of Virtual Reality in Manufacturing
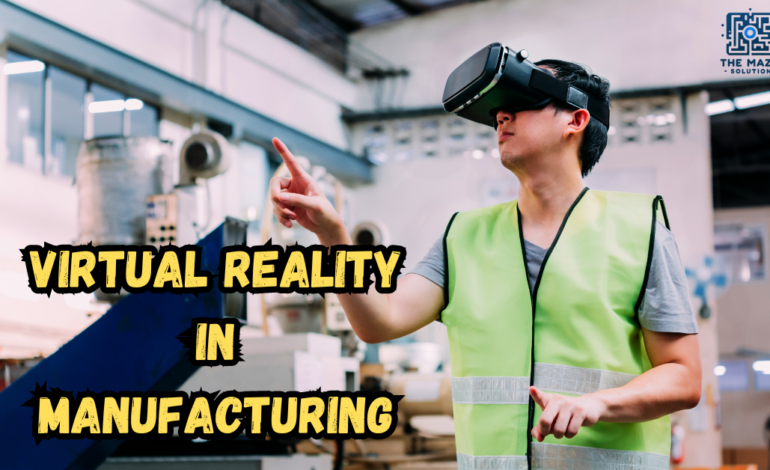
In a world where technology is advancing at a rapid pace, staying ahead in the manufacturing industry requires innovative approaches. One such cutting-edge technology making waves is virtual reality (VR). Once confined to the realms of gaming and entertainment, VR has now entered the manufacturing sector, promising to revolutionize processes and enhance efficiency. This blog will explore the applications and benefits of VR in manufacturing, offering insights for professionals, enthusiasts, and innovators eager to leverage this technology.
Understanding Virtual Reality in Manufacturing
Definition and Scope of Virtual Reality in Manufacturing
Virtual reality in manufacturing is an advanced technological approach that involves the creation of immersive, computer-generated environments designed to replicate real-world manufacturing processes. This cutting-edge technology allows manufacturers to interact with and manipulate virtual models of their products, machinery, and operational workflows within a controlled, simulated space. By offering a lifelike representation of physical environments, VR enables engineers, designers, and production teams to visualize, design, test, and optimize various aspects of their manufacturing processes before they are implemented in the real world.
Historical Context and Evolution
Initially, the use of VR in manufacturing was largely confined to training and visualization purposes. For example, Virtual Reality in manufacturing was utilized to create training simulations for workers to practice complex or dangerous tasks without the risk of real-world consequences. It also allowed engineers and designers to visualize and present their ideas in a more interactive way, providing a clear understanding of how products would look and function.
However, as VR technology has advanced, its applications in manufacturing have expanded significantly. Modern VR systems offer high levels of interactivity and realism, making them invaluable tools for a wide range of applications beyond training. Today, VR is integrated into every stage of the manufacturing process, from product design and development to process optimization, maintenance, and beyond. The ability to simulate entire production lines and factory layouts in a virtual environment is revolutionizing how manufacturers approach problem-solving and innovation.
The Role of VR in Digital Transformation
In the current era of digital transformation, VR has become a key component in the drive towards smarter, more efficient manufacturing processes. The adoption of VR technology is helping manufacturers address several critical challenges, such as reducing production costs, minimizing errors, and accelerating time-to-market for new products. By offering a virtual platform for prototyping, VR reduces the need for physical prototypes, saving both time and resources.
Moreover, VR enhances collaboration among different teams, especially in global manufacturing operations where stakeholders may be located in various parts of the world. Through VR, team members can immerse themselves in the same virtual environment, regardless of their physical location, allowing for real-time collaboration and decision-making. This level of interaction is particularly beneficial in the design and planning stages, where visualizing complex processes and interactions is crucial for making informed decisions.
Expanding Scope of VR in Manufacturing
The scope of VR in manufacturing is continually expanding as new applications and technologies emerge. VR is now being used for detailed process simulations, allowing manufacturers to test different production scenarios and identify potential bottlenecks or inefficiencies before they occur in the real world. This proactive approach helps in optimizing production lines, improving product quality, and reducing waste.
Additionally, VR is playing a vital role in the integration of Industry 4.0 technologies, such as the Internet of Things (IoT), artificial intelligence (AI), and big data analytics. By combining VR with these technologies, manufacturers can create more intelligent and responsive production systems that can adapt to changing demands and conditions in real-time.
Key Applications of Virtual Reality in Manufacturing
Product Design and Development
VR has revolutionized product design by offering a 3D virtual space for prototyping. Designers can create detailed models and simulate their performance in real-world scenarios without incurring the costs and time associated with physical prototypes. Companies like Ford and Boeing have used VR extensively to streamline their design processes, resulting in faster product development cycles and higher-quality outcomes.
In the realm of product development, VR allows for iterative testing and refinement, enabling designers to identify potential issues early on. This proactive approach minimizes costly errors and accelerates the path from concept to market.
Virtual Reality in Manufacturing Process Optimization
Manufacturers use VR to optimize production processes through detailed simulations. By visualizing the entire production line in a virtual environment, managers can identify bottlenecks, test different configurations, and implement changes without disrupting ongoing operations. This level of insight leads to significant improvements in efficiency and cost savings.
Training and development also benefit from VR in manufacturing. Employees can gain hands-on experience in a risk-free environment, enhancing their skills and preparedness for real-world scenarios. For example, companies like Siemens have integrated VR into their training programs, resulting in more competent and confident employees.
Virtual Reality for Maintenance and Repair
Predictive maintenance is another critical application of VR in manufacturing. By using VR to simulate equipment conditions and predict potential failures, manufacturers can perform maintenance tasks proactively, reducing downtime and extending the lifespan of machinery. This approach not only saves costs but also ensures smoother operations.
VR enhances the efficiency of repair and maintenance operations by providing technicians with immersive, step-by-step guides. These virtual instructions improve accuracy and speed, reducing the likelihood of errors and enhancing overall productivity.
Enhancing Collaboration and Communication with VR
VR is an excellent tool for improving teamwork and collaboration in manufacturing. By enabling teams to interact in a shared virtual space, VR fosters cross-departmental collaboration and aligns efforts toward common goals. This capability is particularly valuable for global manufacturing teams, where communication barriers often hinder progress.
Companies like General Electric have leveraged VR to facilitate collaborative workshops and design reviews, allowing participants to visualize concepts and provide feedback in real-time. This approach leads to more informed decisions and streamlined project timelines.
Benefits of Virtual Reality in Manufacturing
Improving Efficiency and Productivity
One of the most significant benefits of VR in manufacturing is its ability to improve efficiency and productivity. By simulating production processes, manufacturers can identify and rectify inefficiencies, reducing production time and costs. This data-driven approach minimizes errors and enhances precision, resulting in higher-quality products.
The reduced need for physical prototypes and real-world testing further contributes to cost savings. Manufacturers can allocate resources more effectively, focusing on innovation and value creation.
Enhancing Safety and Risk Management
Safety is paramount in manufacturing environments, and VR contributes significantly to safety training and risk assessment. By immersing employees in realistic scenarios, VR enhances their ability to identify and respond to potential hazards. This proactive approach reduces the likelihood of workplace accidents and injuries, creating a safer working environment.
Examples abound of VR improving safety in manufacturing plants. Companies like Toyota use VR simulations to train employees on emergency procedures, ensuring they are well-prepared to handle critical situations.
Reducing Costs and Waste
VR offers substantial cost-saving benefits for manufacturers. By minimizing the need for physical prototypes and optimizing production processes, companies can reduce material waste and lower operational costs. This financial impact is further amplified by enhanced product quality and shorter time-to-market.
In addition to financial savings, VR contributes to sustainable manufacturing practices by reducing waste. Manufacturers can explore eco-friendly production methods and materials, aligning with growing environmental responsibilities.
Accelerating Innovation in Manufacturing
VR acts as a catalyst for innovation in manufacturing processes. By providing a platform for experimentation and exploration, VR encourages the development of new techniques and approaches. Manufacturers can push the boundaries of what’s possible, driving continuous improvement and staying ahead of the competition.
Innovative companies like Tesla have embraced VR to revolutionize their manufacturing processes. By simulating assembly lines and production techniques, they have achieved remarkable efficiency gains and product advancements.
Impacts of Virtual Reality in Manufacturing
Long-Term Impacts on the Manufacturing Industry
The long-term impacts of VR on the manufacturing industry are profound. VR is changing the landscape by enabling manufacturers to achieve unprecedented levels of precision, efficiency, and innovation. As the technology continues to evolve, its integration will become a standard practice, driving new trends and opportunities.
Predicted trends include the widespread adoption of VR for training, design, and process optimization. The future of manufacturing will be characterized by more agile and adaptable operations, with VR playing a central role in shaping this transformation.
Economic and Environmental Impacts
The economic implications of adopting VR in manufacturing are significant. Companies that invest in VR technology can expect substantial returns through cost savings, increased productivity, and enhanced product quality. These economic benefits extend to job creation and workforce development, as manufacturers require skilled professionals to operate and manage VR systems.
Environmentally, VR contributes to sustainability efforts by reducing waste and promoting eco-friendly manufacturing practices. Manufacturers can explore renewable energy sources, optimize resource usage, and minimize their carbon footprint, aligning with global sustainability goals.
Challenges and Limitations of Virtual Reality in Manufacturing
Despite its many benefits, VR in manufacturing is not without challenges. Barriers to widespread adoption include the initial investment required for VR infrastructure and the need for specialized skills. Technological challenges, such as hardware limitations and software compatibility issues, also pose obstacles.
To overcome these challenges, manufacturers must adopt strategic approaches. Collaboration with technology providers, investment in employee training, and the implementation of scalable solutions are essential steps toward successful VR integration.
Future Prospects: The Role of VR in Manufacturing Innovation
The Evolution of VR Technologies in Manufacturing
The evolution of VR technologies in manufacturing is set to continue, with emerging trends and innovations on the horizon. The integration of AI and IoT with VR will further enhance its capabilities, enabling manufacturers to collect and analyze real-time data for improved decision-making.
Predictions for the next decade indicate that VR will become an integral part of manufacturing operations. Advances in VR hardware, such as more immersive headsets and haptic feedback devices, will enhance the user experience and drive broader adoption.
Preparing for the Future What Manufacturers Need to Know
Manufacturers must be proactive in preparing for a VR-driven future. Implementing VR successfully requires careful planning and investment. Companies should develop comprehensive strategies that address workforce training, infrastructure requirements, and technological partnerships.
Upskilling the workforce is a critical component of this preparation. Employees need to be equipped with the knowledge and skills to leverage VR effectively. Training programs, certifications, and continuous learning opportunities will empower the workforce to thrive in a VR-driven industry.
Investment strategies are equally important. Manufacturers should allocate resources strategically, focusing on scalable solutions that offer long-term value. By prioritizing VR integration, companies can position themselves as leaders in the evolving manufacturing landscape.
Conclusion
Virtual reality is a game-changer for the manufacturing industry, offering a myriad of applications and benefits. From improving efficiency and safety to accelerating innovation and reducing costs, VR holds the potential to transform how manufacturers operate.
By understanding and harnessing the power of VR, manufacturers can stay ahead of the competition and drive sustainable growth. The time to act is now, as the manufacturing landscape continues to evolve.
For those ready to explore the possibilities of VR in manufacturing, numerous resources and tools are available to guide the way. Collaborating with experts, investing in technology, and fostering a culture of innovation will pave the path to success in this exciting new era of manufacturing.